The importance of bellows in industrial systems
Bellows are essential components in many industrial systems. Their main function is to protect moving parts, absorb vibrations, and prevent the entry of contaminants such as water, dust, or chemicals. They are widely used in sectors such as wastewater treatment (WWTP), heavy machinery, robotics, automotive, and many other applications.
However, it is not uncommon for bellows to fail prematurely. This can lead to unexpected downtime, high repair costs, and the risk of damage to other components. In this article, we explore the five most common causes of premature bellows failure and how you can prevent them to maximize their lifespan.
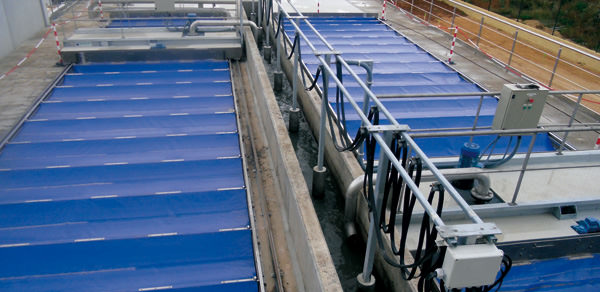
Cause #1 – Incorrect choice of bellows material
One of the most common reasons for a bellows to fail prematurely is the inappropriate choice of material from which it is made. Each working environment requires specific technical properties. Not all materials offer the same resistance to extreme temperatures, chemicals, pressure, or abrasion.
For example, a rubber bellows may be sufficient for basic applications, but if it is exposed to industrial oils, constant friction, or high temperatures, it is best to opt for treated industrial leather or technical polymers such as polyurethane or silicone.
How to avoid this?
Consult with a specialized manufacturer who will analyze the bellows’ environment and use. Choosing the right material from the start can significantly extend its lifespan.
Cause #2 – Extreme Environmental Conditions
Bellows that operate in demanding conditions—such as high temperatures, high humidity, exposure to chemicals, or UV rays—are more susceptible to breakage if they have not been specifically designed for that type of environment.
For example, in WWTPs, bellows are often exposed to corrosive agents and sudden temperature fluctuations. A material not prepared for these conditions can become brittle, deform, or lose its elasticity.
How to prevent this?
Choose materials that are resistant to chemicals, temperatures, and atmospheric agents. In extreme cases, protective coatings can be applied or reinforced bellows can be used.
Cause #3 – Incorrect Bellows Installation
Improper installation is another common cause of premature failure. A bellows that is misaligned, overtight, or not properly secured can become deformed, pinched, or cut during machine operation.
Common errors include the use of inappropriate clamps, incorrect distances between fixing points, or a lack of tightness testing after installation.
How to avoid it?
Follow the manufacturer’s recommendations, respect design tolerances, and, if possible, request the assistance of a specialized installation technician.
Cause #4 – Lack of Regular Maintenance
Although bellows are designed to resist wear, they require regular monitoring. Dirt accumulation, prolonged exposure to contaminants, or small, unrepaired cracks can drastically reduce their lifespan.
How to prevent it?
Establish a preventive maintenance plan. Perform frequent visual inspections and replace bellows if you detect signs of fatigue, hardening, or uneven wear.
Cause #5 – Intensive Use or Use Outside of Technical Specifications
Each bellows has a defined operating range: maximum load, internal pressure, movement cycles, or expansion rate. Using it beyond these limits accelerates its deterioration.
For example, using a bellows designed for 1,000 cycles per hour on a machine that performs 5,000 will inevitably cause premature failure.
How to avoid this?
Make sure the bellows are adapted to the actual work rate and demands. If the application is demanding, request a reinforced or customized design.
How to avoid premature failure of your bellows?
The best way to prevent failure is a combination of prevention, technical knowledge, and specialized advice. From proper material selection to professional assembly and a maintenance plan, every step counts.
Working with certified and experienced manufacturers, such as Lluis Creus S.L., guarantees products adapted to your application, manufactured with quality criteria under regulations such as ISO 9001:2015.
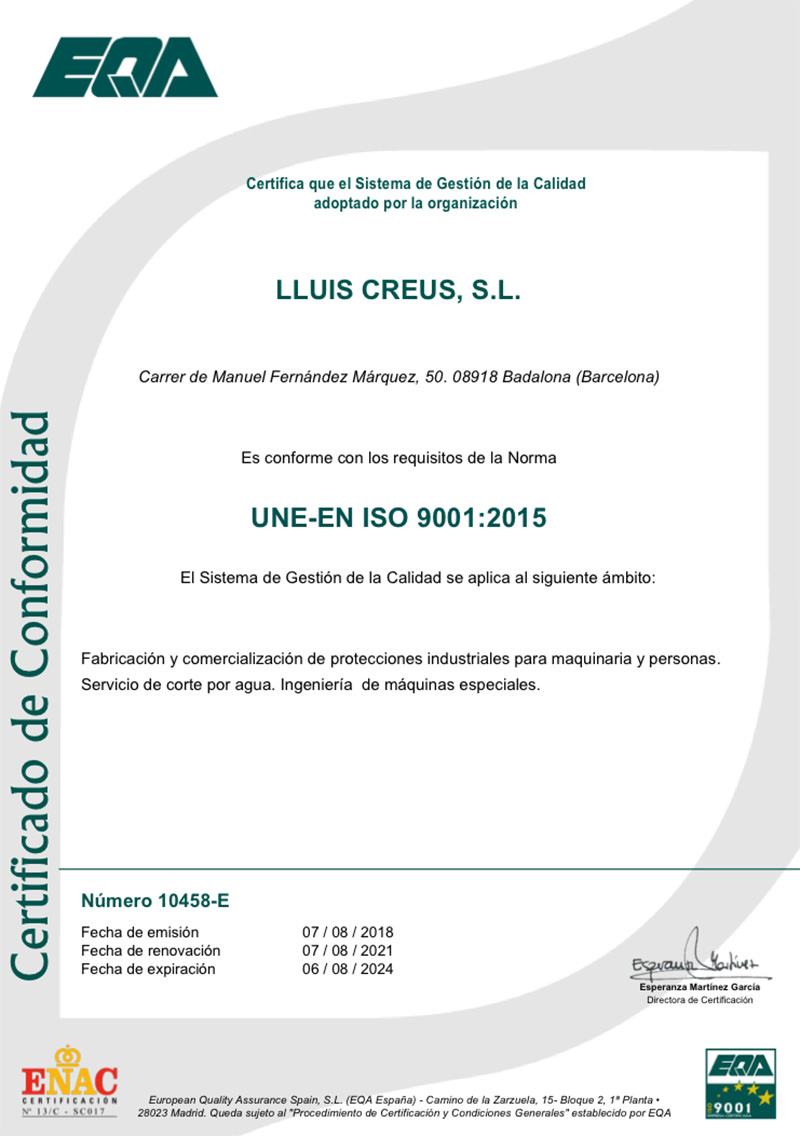
Lluis Creus S.L.: experts in custom bellows manufacturing
With over 140 years of experience, at Lluis Creus S.L. we are leaders in the manufacture of custom industrial bellows, especially for applications in wastewater treatment plants (WWTPs) and industrial machinery.
We are the only industrial leather handlers in Catalonia and use technologies such as waterjet and laser cutting to ensure precision and durability.
We are also ISO 9001:2015 certified, ensuring consistent quality in every project.