In industrial sectors and applications where harsh conditions are the norm, specialized bellows have become an essential component to ensure the proper functioning of machinery and equipment. Designed to withstand extreme temperatures, humidity, and aggressive chemicals, these elements offer a reliable solution in extreme environments. In this article, we will explain how these bellows are transforming demanding industries and the key advantages of their advanced design.
What are specialized bellows?
Bellows are flexible devices that protect sensitive mechanical components, such as hydraulic cylinders, spindles, and shafts, from external contaminants. In extreme environments, where environmental conditions can compromise the operation of equipment, specialized bellows are essential to prevent damage, prolong the life of parts, and ensure consistent performance.
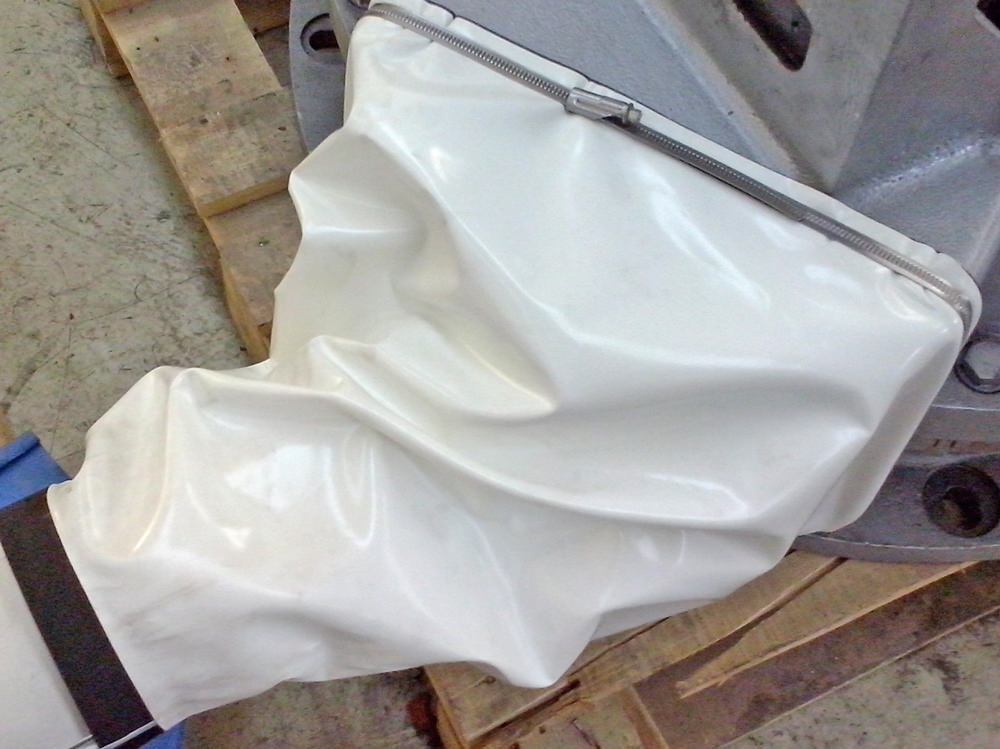
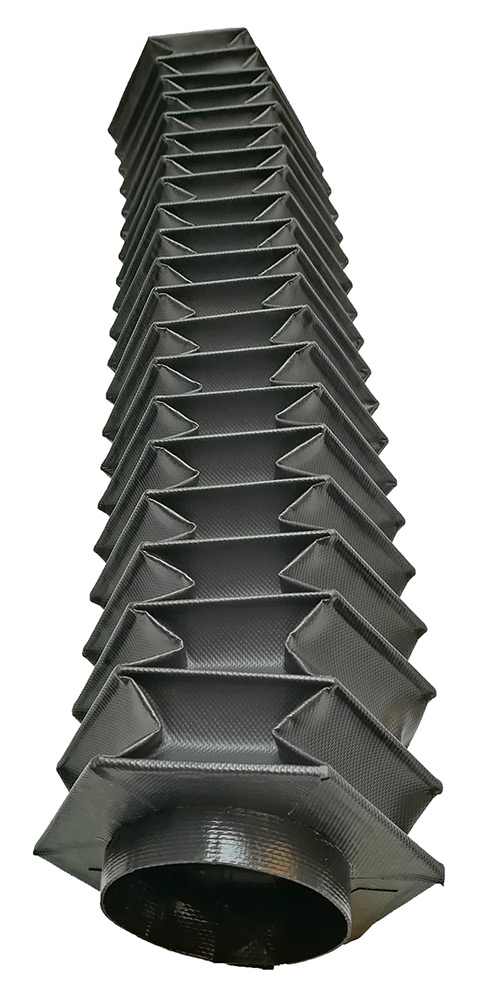
Features of bellows for extreme environments
Bellows designed for harsh conditions incorporate advanced materials and technologies that make them highly resistant. Some of their most notable features include:
1. Resistance to extreme temperatures
● High temperatures: They use materials such as silicone or advanced elastomers that withstand temperatures that can exceed 200 °C.
● Low temperatures: In cryogenic applications, certain bellows can operate in environments below -50 °C without losing flexibility.
2. Humidity and water tolerance
Specialized bellows are designed for environments with high humidity or direct immersion in liquids. Thanks to specific coatings or waterproof materials, they offer protection against corrosion and deterioration.
3. Chemical resistance
For chemical or pharmaceutical industries, bellows must be able to withstand contact with aggressive substances such as acids, bases or solvents without degrading. Compounds such as PTFE (Teflon) or fluorinated polymers are ideal materials in these cases.
4. Protection against particles and abrasion
In applications where dust, sand or abrasive particles are present, bellows provide a shield that prevents premature wear of key components.
Main applications of specialized bellows
1. Aerospace industry
In propulsion and control systems, bellows protect mechanisms from extreme temperature fluctuations and exposure to fuel-derived chemicals.
2. Medical sector
Bellows used in medical equipment must be resistant to aggressive cleaning chemicals and offer a high degree of sterilization.
3. Energy and oil
On oil platforms and gas extraction systems, bellows face harsh conditions with continuous exposure to corrosive substances and extreme temperatures.
4. Automotive and railway industry
They protect suspension systems, brakes and other mechanisms from abrasive particles, humidity and severe thermal variations.
Advantages of specialized bellows
Investing in high-quality bellows designed for extreme environments offers significant benefits:
- Increased durability: They reduce maintenance costs by minimizing wear on key components.
- Operational efficiency: They keep equipment running optimally even under harsh conditions.
- Regulatory compliance: Many of these bellows comply with strict safety and hygiene regulations, especially in sectors such as food and pharmaceuticals.
- Customization: Bellows can be custom-designed to fit specific needs, ensuring perfect compatibility with machinery.
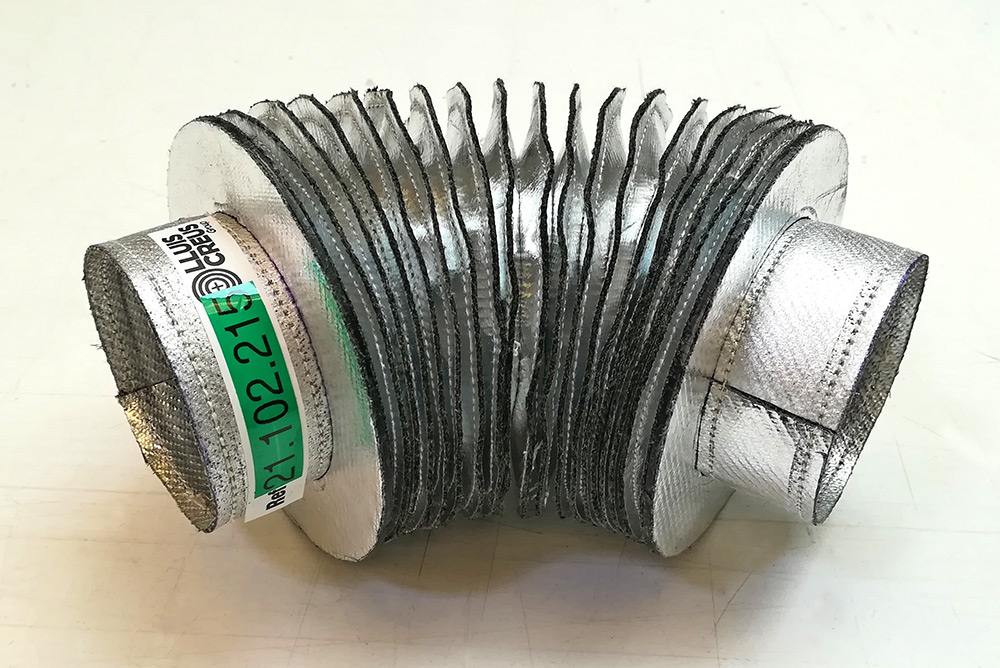
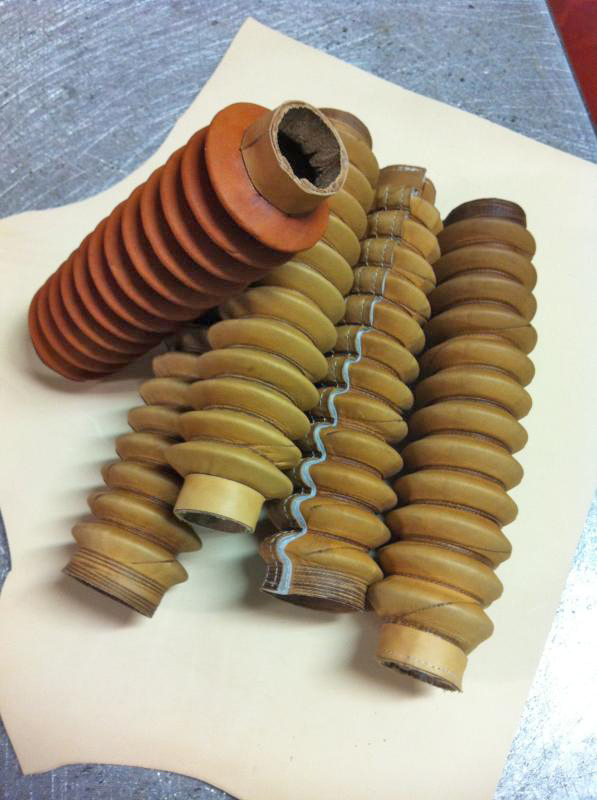
Conclusion
Specialized bellows for extreme environments represent an indispensable solution to protect critical equipment in harsh conditions. Thanks to their advanced design and materials, they offer resistance to extreme temperatures, aggressive chemicals and humidity, ensuring optimal performance in the most challenging applications.
In a world where reliability and regulatory compliance are essential, specialized bellows not only ensure the correct operation of equipment, but also contribute to the sustainability and efficiency of industrial processes. If you are looking to maximize the lifespan of your machinery in extreme environments, consider implementing these components as a strategic investment.