Introduction
Wastewater treatment plants are highly demanding industrial environments. Equipment such as pumps, compressors, agitators, and valve systems must operate under extreme conditions of humidity, aggressive chemicals, and abrasive particles.
In this context, machinery bellows become critical protection elements. Their function is to preserve the integrity of sensitive moving parts, prevent contamination, and maximize the equipment’s lifespan.
Throughout this article, we will explore why industrial bellows are so important in water treatment plants, what types exist, how to choose the most appropriate one, and what mistakes to avoid.
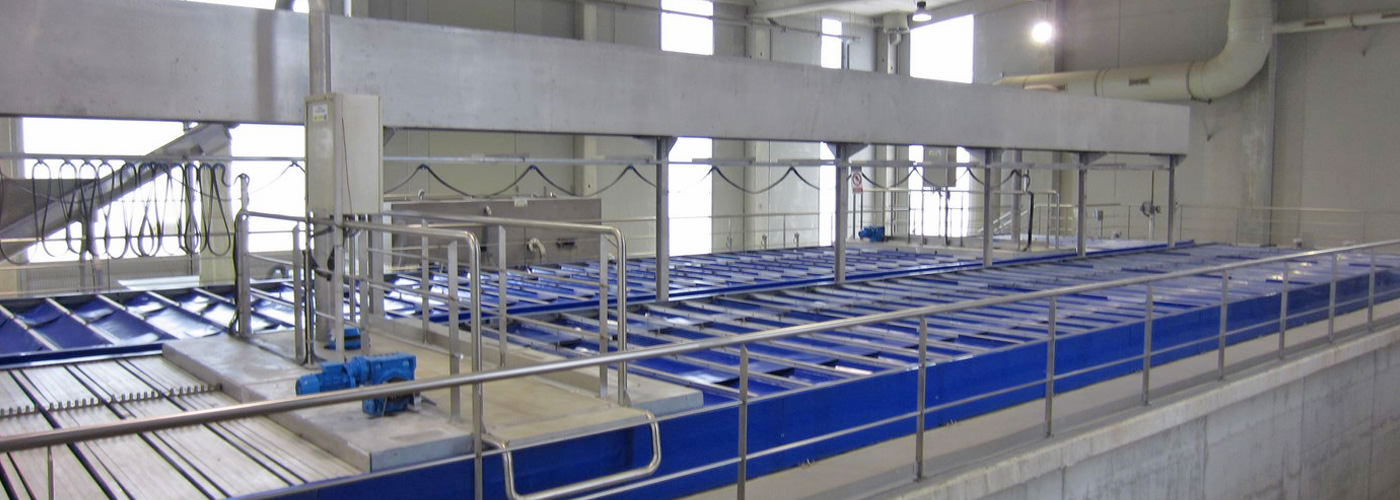
Why are machinery bellows essential in water treatment plants?
Treatment plants expose their machines to:
● Constantly high humidity.
● Chemical contamination of various types.
● Abrasion from suspended solids or sediments.
● Accelerated corrosion of metal parts.
Machinery bellows act as a flexible barrier that:
● Isolates moving parts such as shafts, spindles, or pistons.
● Prevents the ingress of corrosive or abrasive agents.
● Reduces premature wear of essential components.
● Facilitates maintenance by keeping critical surfaces clean.
In short, a properly installed bellows can double or triple the lifespan of certain components.
Main equipment requiring bellows in water treatment plants
In a wastewater treatment plant, protective bellows are required for multiple pieces of equipment, including:
● Slurry pumps: protect shafts and dynamic seals.
● Automatic valve systems: protect actuators and spindles.
● Industrial agitators: cover moving parts exposed to aggressive media.
● Air compressors: protect cylinders and valves from dust and moisture.
● Solids conveying systems: protect transmission mechanisms.
Each application presents specific risks that require a bellows tailored in material, size, and design.
Types of bellows for water treatment plants
There are several types of industrial bellows suitable for these conditions:
● Reinforced PVC bellows: excellent chemical and mechanical resistance.
● Neoprene bellows: high abrasion resistance and elasticity.
● Polyurethane bellows: combine flexibility with high resistance to oils and chemicals.
● Heat-sealed bellows: seamless solutions, ideal for maximum tightness.
The correct selection depends on the type of fluid treated, operating temperatures, and exposure to chemicals.
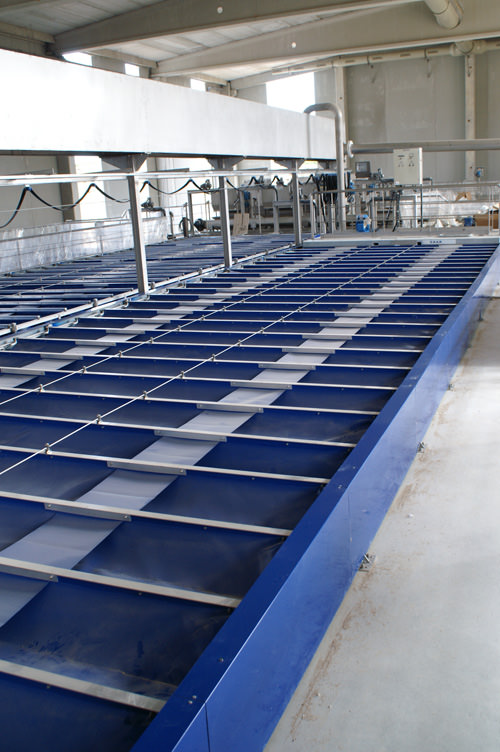
Key factors for selecting bellows in wastewater treatment plants
When choosing a bellows for machinery in wastewater environments, consider:
● Chemical compatibility: resistance to the type of effluent present.
● Impermeability: ability to prevent the entry of liquids or vapors.
● Abrasion resistance: especially in areas of contact with solids.
● Mechanical flexibility: to handle repetitive movements without failure.
● Ease of installation and maintenance: avoid long downtimes.
A mistake in bellows selection can lead to costly breakdowns and unscheduled downtime.
Ideal materials for bellows in wastewater treatment
Material | Advantages |
Reinforced PVC: | Balanced chemical and mechanical resistance. |
Neoprene: | Superior elasticity and wear resistance. |
Polyurethane: | High durability against oils and chemicals. |
PTFE (Teflon): | Maximum resistance to aggressive chemicals, less flexible. |
The choice will depend on the balance between cost, lifespan, and environmental exposure.
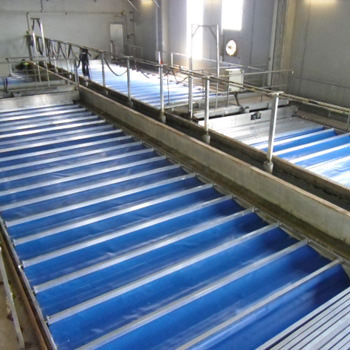
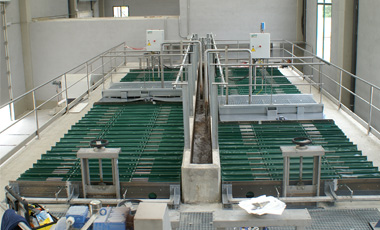
Benefits of using bellows in water treatment plants
Implementing industrial bellows offers very specific benefits:
● Greater protection of critical components.
● Reduction in maintenance and replacement costs.
● Increased machinery uptime.
● Compliance with environmental and safety regulations.
● Reduction in the risk of unplanned downtime.
In industries where downtime is very costly, bellows represent a simple yet powerful solution.
Common mistakes in bellows selection and installation
Avoid these pitfalls:
● Underestimating the aggressiveness of the chemical environment.
● Using non-waterproof materials in high-humidity areas.
● Not considering the dynamic motion of the protected shaft or component.
● Incorrect installations that leave leaks.
A bad bellows, or one installed incorrectly, can cause more problems than it solves.
Trends in bellows design for industrial applications
The future of bellows for machinery in harsh environments such as treatment plants points toward:
● Hybrid materials with self-healing properties.
● Smart bellows with integrated wear sensors.
● Adaptive dynamic sealing systems.
The combination of extreme chemical resistance and sensorization will open a new era in industrial machinery protection.
Bellows maintenance in water treatment plants
Proper maintenance ensures long-term bellows effectiveness:
● Regular inspections: look for wear, cracks, or leaks.
● Controlled cleaning: remove sediment or chemical buildup.
● Preventive replacement: don’t wait for critical failures.
Including bellows in the plant’s maintenance plan is essential.
Conclusion: Protect your investment with the right bellows
Wastewater treatment plants are unforgiving environments for any machinery. Without proper protection, maintenance, repair, and downtime costs can skyrocket.
Incorporating industrial machinery bellows, specifically designed for these conditions, is not an expense, but an investment in reliability and efficiency.
Do you need personalized advice to select the best bellows for your plant?
Contact us now and protect your equipment as it deserves.