Why are industrial protective covers important?
Industrial protective covers are designed to cover and protect sensitive parts of machinery, such as cylinders, guides, cables, and connectors. Their function is to act as a barrier against external agents that can damage internal components: dust, liquids, chemicals, high temperatures, or mechanical impacts.
Implementing covers in industrial environments not only prevents failures and unplanned downtime, but also increases the overall durability and efficiency of equipment. In demanding sectors, these covers are not an accessory, but an operational necessity.
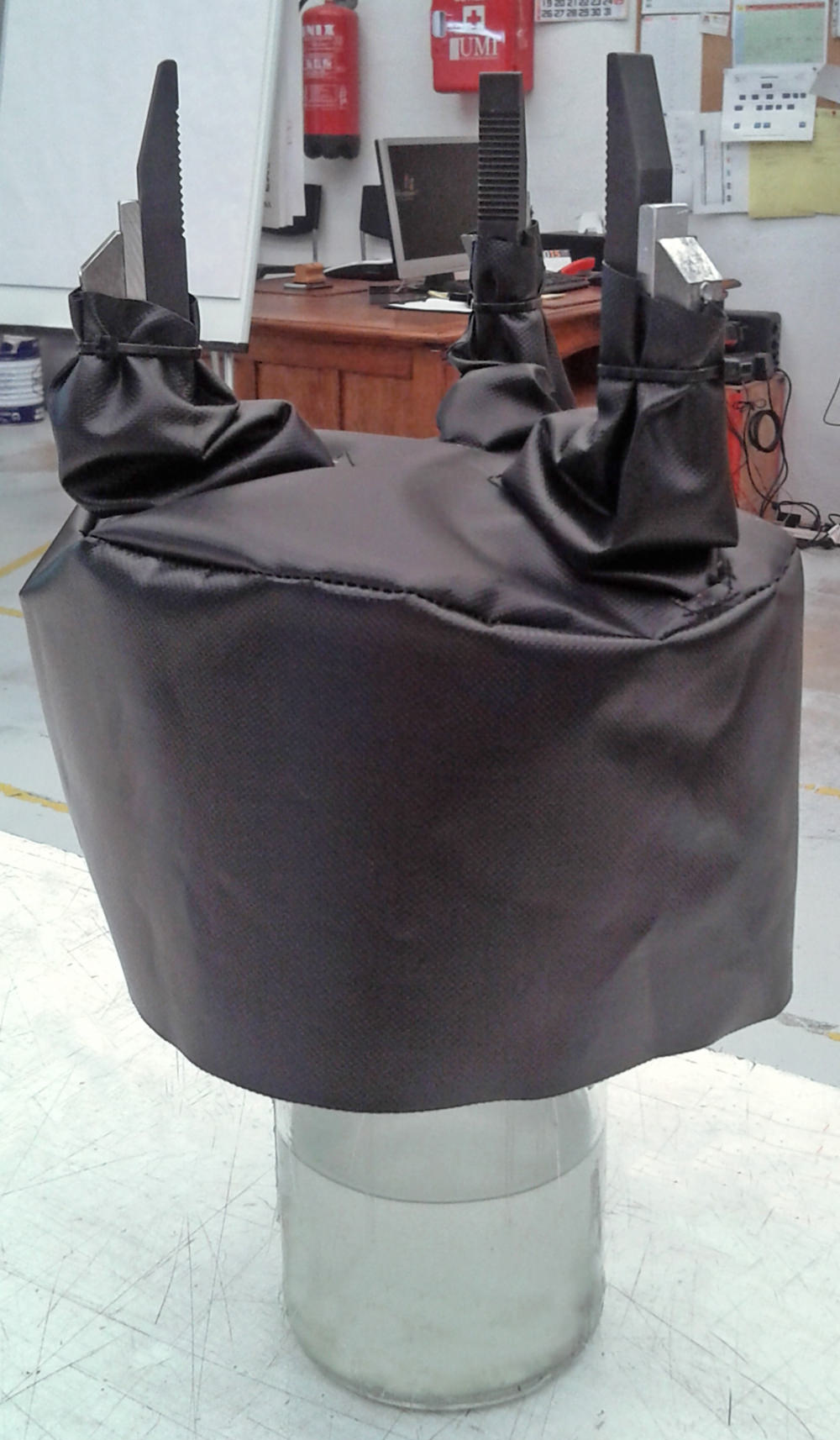
Key Functions of Industrial Protective Covers
Industrial covers perform several essential functions for proper machine operation:
- Mechanical protection: They prevent damage from impacts, friction, abrasion, or contact with other moving parts.
- Insulation against contaminants: They prevent the entry of dust, water, grease, chemical residues, and other aggressive agents.
- Performance optimization: By keeping the protected parts clean and in good condition, they contribute to the sustained performance of the machinery.
- Reduction in corrective maintenance: By providing constant protection, urgent and costly interventions are reduced.
Common Materials in Industrial Covers
The choice of the right material depends on the environment, application, and frequency of use. The most commonly used are:
- Industrial leather: High wear resistance, excellent performance in environments with friction and varying temperatures.
- PVC and engineering plastics: Ideal for environments with humidity, mild chemicals, or where visibility is required.
- Rubber, neoprene, and silicone: widely used in applications requiring flexibility, thermal insulation, or protection from harsh chemicals.
Each material has its advantages, and the key is selecting the one that best suits the specific application.
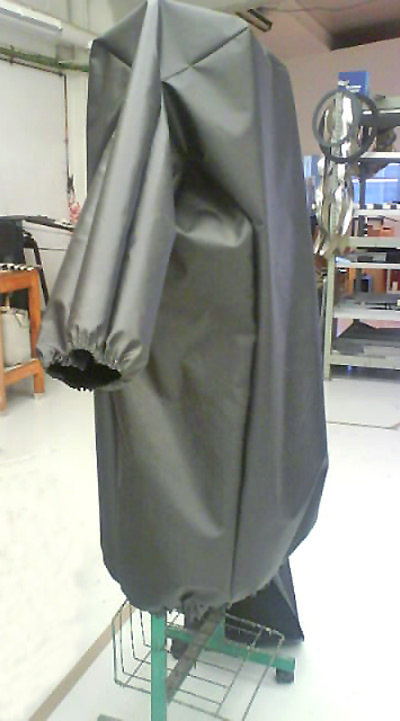
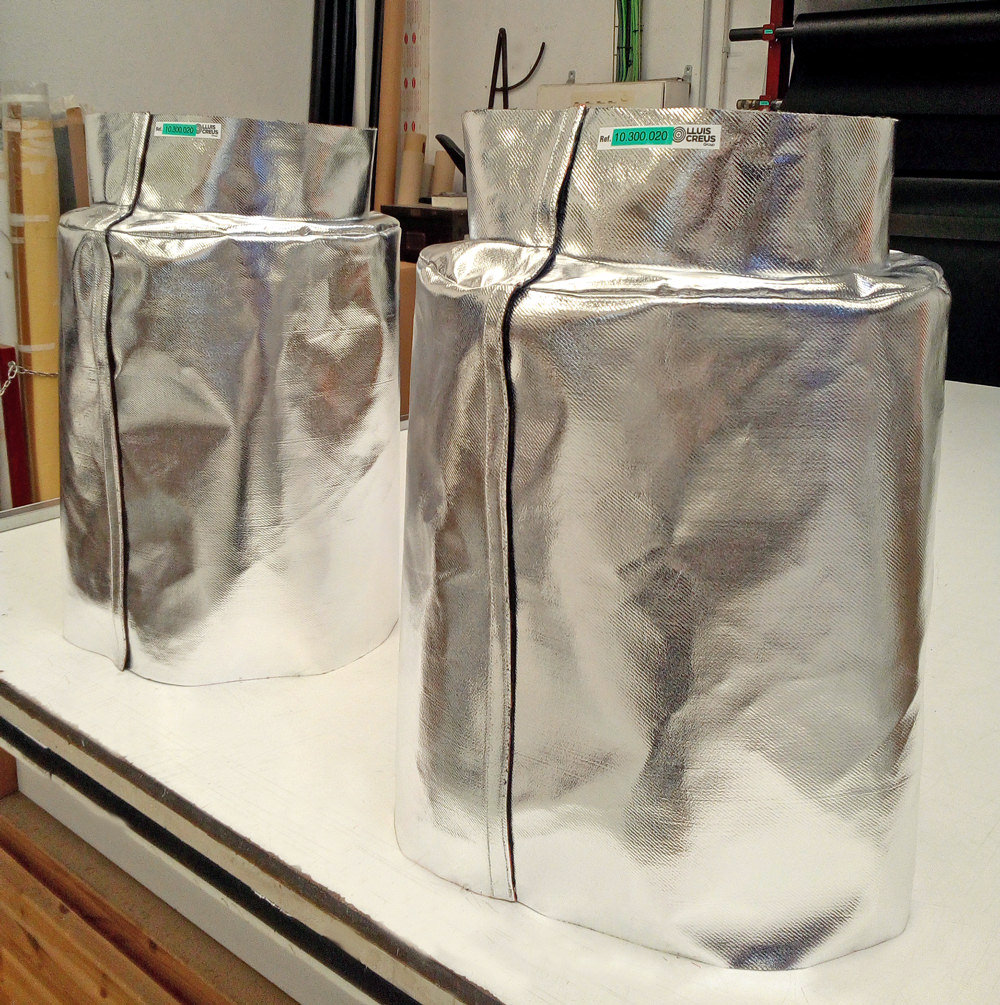
Types of industrial protective sleeves by application
Sleeves can be adapted to different parts and needs. Some common types include:
-
Sleeves for hydraulic and pneumatic cylinders: protect the rod and seals from contamination and impacts.
-
Sleeves for screw drives and linear guides: prevent the accumulation of particles that can cause friction or wear.
-
Sleeves for cables, hoses, or electrical connectors: prevent cuts, burns, or short circuits caused by harsh environments.
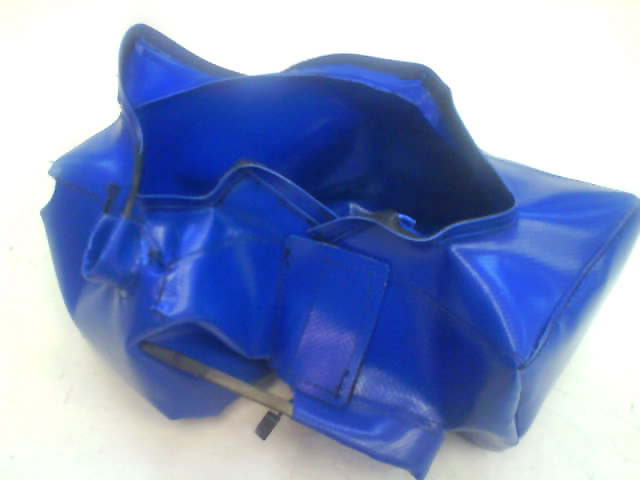
Sectors that most use industrial protective covers
These solutions are widely used in sectors where machinery is exposed to complex conditions:
- WWTPs (water treatment plants): to prevent corrosion and contact with sludge and gases.
- Food industry: to maintain cleanliness and facilitate hygienic processes.
- Automotive and heavy machinery: to reduce wear due to dust, oil, or constant vibration.
- Railways and the energy sector: where equipment is exposed to the outdoors or subject to high workloads.
Custom covers vs. standard covers
Although standard solutions exist on the market, more and more industries are opting for custom covers that perfectly fit their needs.
Advantages of a custom cover:
- Better fit and seal.
- Greater durability and resistance.
- Adaptability to the type of movement and specific environment.
- Optimization of maintenance and replacement
Considerations when choosing a protective cover
Before purchasing a cover for your equipment, it is important to consider:
- Environmental conditions: temperature, humidity, presence of chemicals or particles.
- Type and frequency of movement: linear displacement, rotation, expansion, etc.
- Ease of installation and disassembly: important for inspection and cleaning tasks.
- Compatibility with other equipment parts or protections.
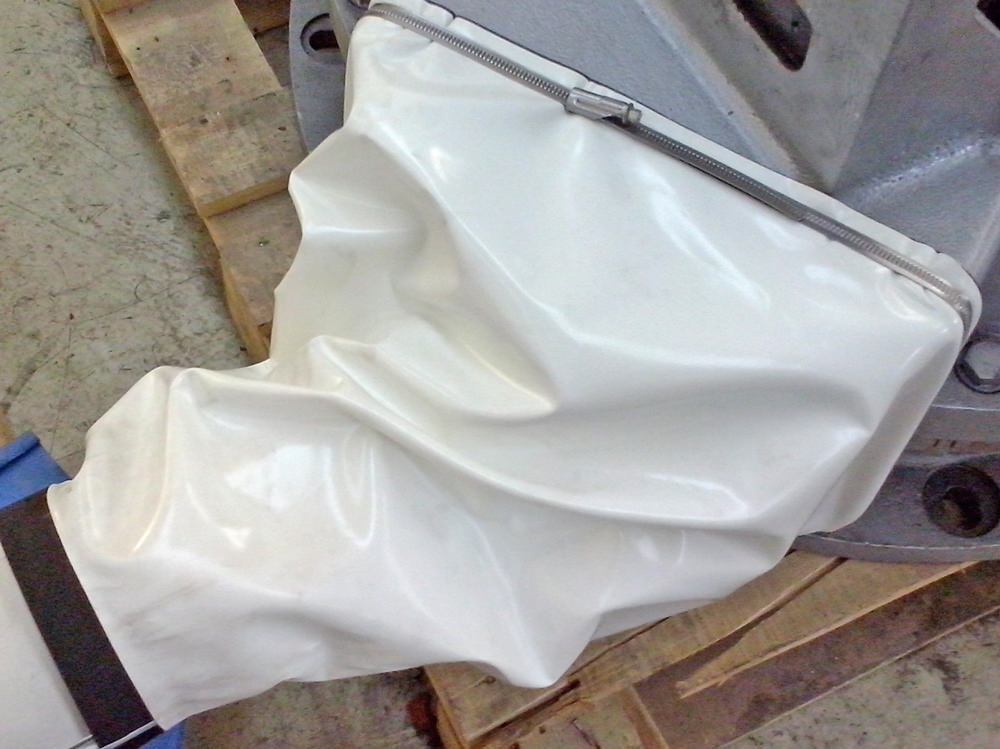
Advantages of implementing protective covers on your machinery
Integrating industrial covers on your equipment has multiple benefits:
- Fewer breakdowns and unplanned downtime.
- Greater durability of cylinders, guides, connectors, and other components.
- Savings in corrective maintenance.
- Greater safety for personnel operating the machines.
In short, they are a smart investment in productivity and operational sustainability.
Maintenance recommendations for industrial covers
Like any technical component, covers also require care:
- Regular cleaning with mild products.
- Monthly inspection for wear, cracks, or hardening.
- Immediate replacement in case of visible damage.
Preventive maintenance helps maintain their protective function for longer.