The strategic importance of industrial bellows
In highly demanding industrial environments, industrial bellows are a critical component in protecting moving parts such as screws, guides, actuators, and shafts.
Their proper operation is essential for:
● Maintaining the mechanical integrity of systems.
● Preventing contamination of critical areas.
● Reducing exposure to abrasives, fluids, or chemical agents.
Despite their relatively low cost, a failure in an industrial bellows can lead to:
● Severe mechanical damage to high-investment components.
● Unforeseen increases in maintenance costs.
● Significant reductions in machine availability.
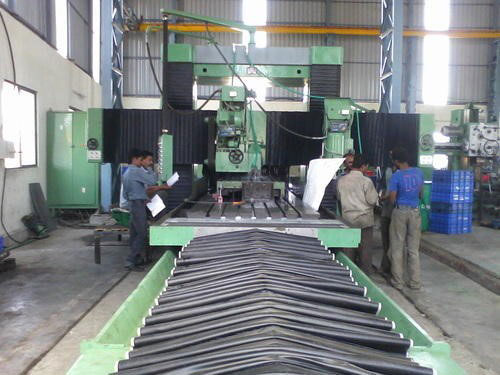
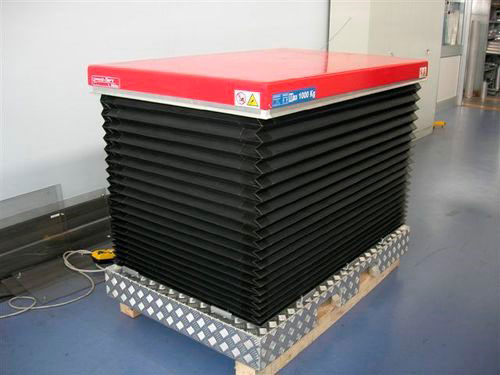
Technical problems arising from poor industrial bellows design
When an industrial bellows is not properly adapted to the actual working environment, failures such as:
Cause | Operational consequence |
Material incompatible with the environment | Chemical degradation and premature failure |
Inadequate fold geometry | Cyclic fatigue failure |
Inaccessible or inadequate fasteners | Increased intervention and maintenance times |
Insufficient protection against solid or liquid contaminants | Accelerated damage to guides, shafts, and screws |
These problems generate hidden costs that directly impact the plant’s operational efficiency.
Why is it critical to redesign industrial bellows?
Industrial bellows redesign responds to the need to:
● Update protection following changes in operating conditions (higher speeds, different contaminants, new safety regulations such as ISO 14120 or ISO 13849).
● Align preventive maintenance with the actual operation of the machinery.
● Reduce the total cost of ownership (TCO) of productive assets.
Failure to adapt the bellows design generates increasing additional costs for corrective maintenance, labor, and replacement of critical components.
Technical methodology for redesigning an industrial bellows
The optimization process should include:
1. Analysis of actual operating conditions
● Identification of work cycles: linear, angular, or combined movements.
● Measurement of maximum speeds, accelerations, and temperatures.
● Assessment of exposure to chemicals, abrasives, humidity, or high temperatures.
2. Precise selection of bellows material
● Industrial PVC: good general chemical resistance, suitable for high humidity.
● Technical polyurethane: ideal for intense abrasion and dynamic loads.
● Neoprene: excellent elasticity for high-frequency cyclic movements.
● PTFE (Teflon): maximum resistance to aggressive chemicals, although less flexible.
3. Geometric optimization
● Redesign of the number, height, and radius of folds to adapt them to the dynamic cycle.
● Minimization of bending stresses to extend service life.
4. Improved accessibility
● Incorporation of industrial zippers or quick-release fasteners.
● Modular assembly systems that reduce MTTR (Mean Time to Repair).
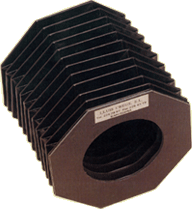
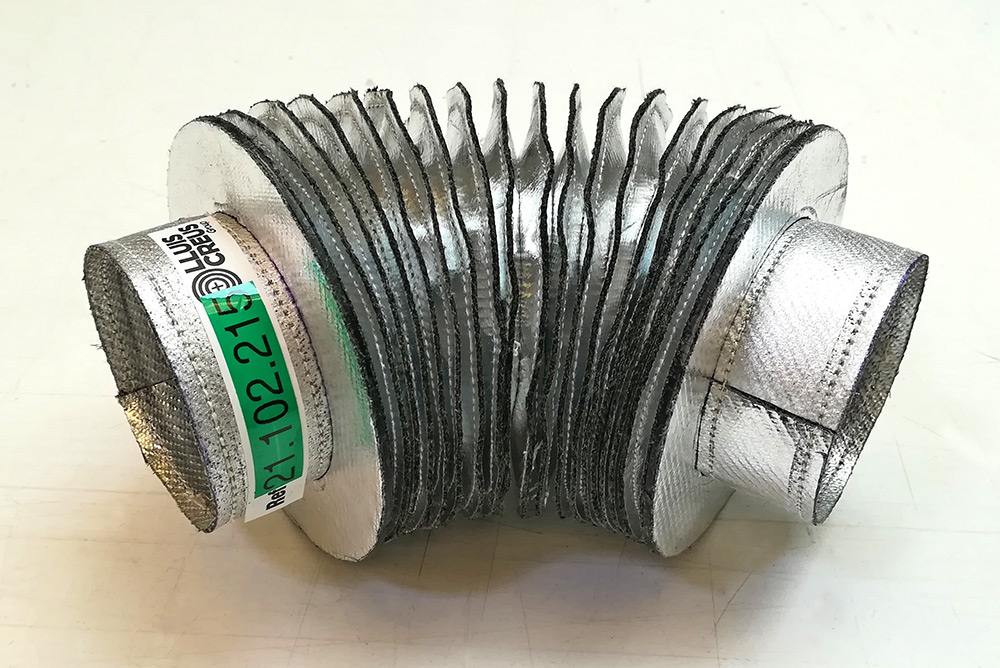
Documented results of industrial bellows redesign
Based on field studies and industrial audits:
Indicator | Average improvement after redesign |
Industrial bellows lifespan | +150% a +250% |
Annual maintenance cost reduction | -18% a -24% |
Annual maintenance cost reduction | -30% |
Improved operational availability (OEE) | +8% a +15% |
These results confirm the high cost-effectiveness of technical redesign compared to reactive maintenance.
Technical checklist to evaluate the need for industrial bellows redesign
Before making strategic decisions, it is necessary to analyze:
● Does the current bellows material adequately resist the agents present in the plant?
● Have speeds or operating cycles increased compared to the initial stage?
● Are there records of repetitive failures in elements protected by bellows?
● Do maintenance interventions on the bellows extend downtime?
An affirmative answer to two or more questions justifies studying the redesign as an optimization project.
Conclusion
In today’s industrial context, where every hour of production counts, the industrial bellows is moving from being an accessory component to becoming a strategic protection asset.
Redesigning an industrial bellows in a technically justified manner:
● Minimizes preventive and corrective maintenance costs.
● Extends the useful life of critical machinery.
● Improves operational reliability.
● Reduces unscheduled downtime.
For industrial maintenance and purchasing managers, addressing bellows redesign is not an option, but a decision based on efficiency, costs, and competitiveness.
Request a professional technical diagnosis and optimize the performance of your industrial plant.