The Importance of Maintenance in Bellows Systems
Bellows are essential components in many industrial installations, especially in environments such as wastewater treatment plants (WWTPs), machinery with moving parts, or hydraulic and pneumatic systems. Their primary function is to protect delicate mechanisms, allow flexible movement, and maintain tightness against external elements.
However, if proper maintenance is not performed, bellows can deteriorate prematurely, leading to costly breakdowns, unplanned downtime, and operational risks. Therefore, implementing a monthly maintenance checklist is a simple yet crucial measure to ensure operational continuity and safety.
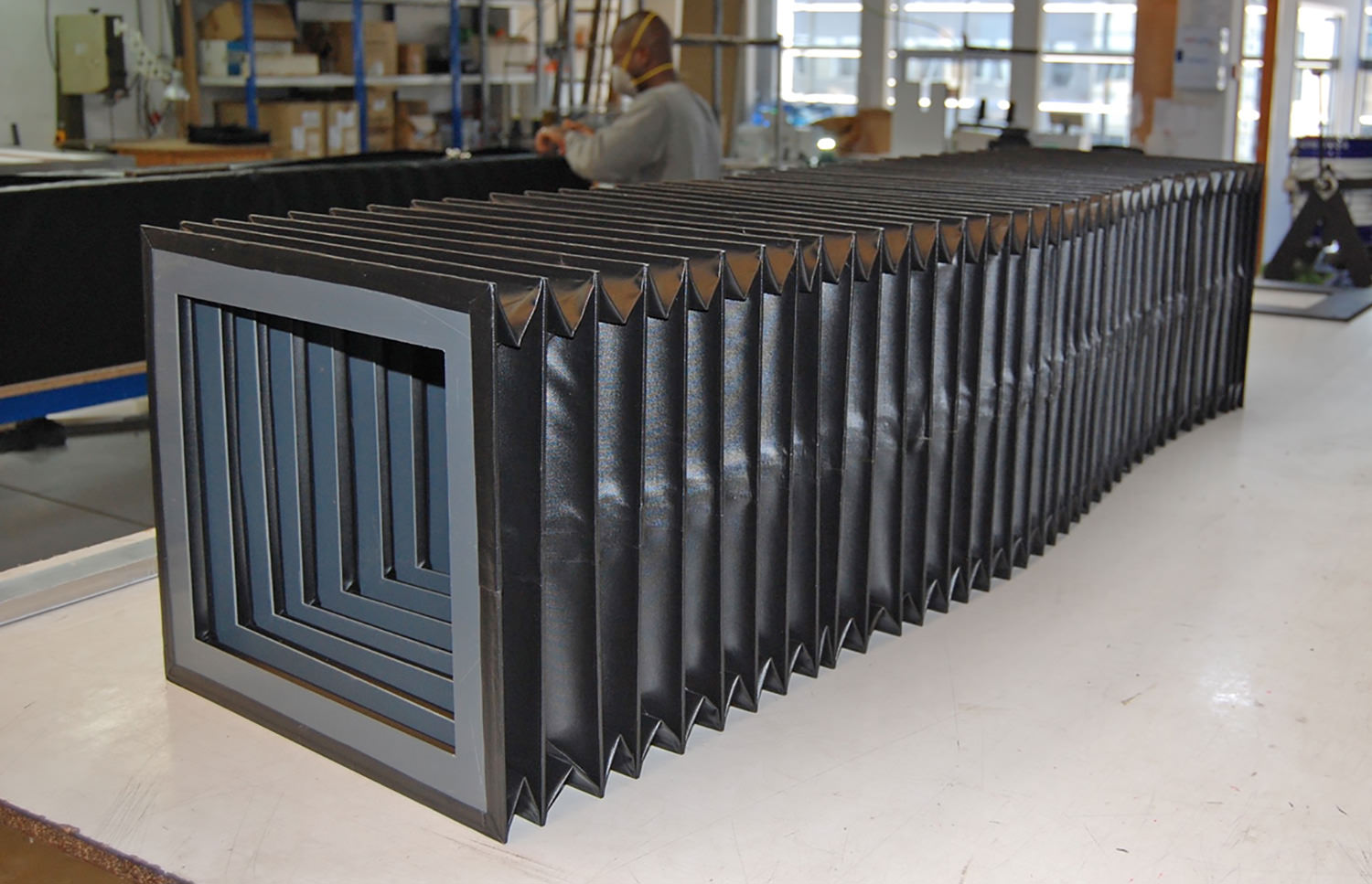
Benefits of performing a monthly bellows inspection
Adopting a monthly inspection routine offers multiple advantages:
● Reduction in unexpected failures: Detecting small cracks or wear early prevents major breakdowns.
● Longer component life: A well-maintained bellows can last for years, even under demanding conditions.
● Operational efficiency: Fewer unplanned downtimes and improved machine performance.
● Cost savings: Avoiding major repairs and frequent replacements reduces long-term costs.
Who should apply this checklist?
This guide is intended for:
● Companies with wastewater treatment plants (WWTPs).
● Industries that use bellows-equipped machinery in environments with dust, humidity, or chemical agents.
● Production plants and workshops that wish to implement preventive maintenance as part of their good operating practices.
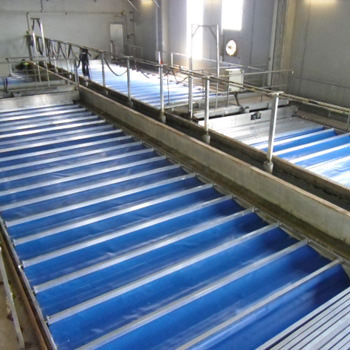
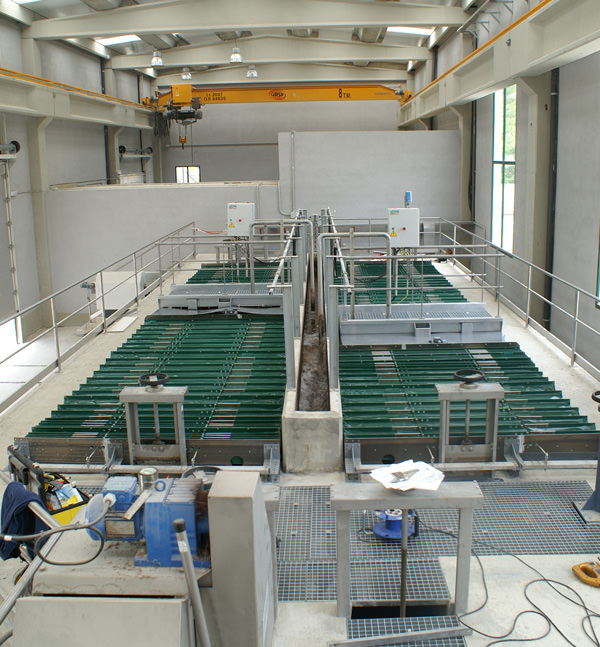
Step-by-step monthly maintenance checklist
1. External visual inspection of the bellows
Check the overall condition of the bellows, observing any cracks, cuts, deformations, hardening of the material, or any signs of unusual wear.
2. Alignment and tension check
Make sure the bellows are properly positioned and do not show any stretching, excessive folds, or twists that could damage them with use.
3. Surface cleaning
Wipe the entire surface of the bellows with a dry cloth or neutral product. Remove any dust, mud, grease, or chemical residue.
4. Check fasteners and clamps
Check that the clamps, screws, or other fastening systems are securely fastened and show no signs of rust or movement.
5. Leak test (if applicable)
If the bellows acts as a barrier to air, gases, or liquids, perform basic leak tests to detect possible leaks or pressure losses.
6. Documentation of findings and corrective action
Note any anomalies detected and plan their repair or replacement. Recording this data is key to traceability and continuous improvement.
Recommended tools for applying the checklist
To carry out these tasks effectively, it is helpful to have:
● An LED flashlight to observe areas with low visibility.
● A magnifying glass or magnifying lens to detect microcracks.
● Soft cloths and neutral cleaning products.
● A pressure gauge or pressure sensor (if tightness verification is required).
Common mistakes to avoid in bellows maintenance
● Not documenting inspections: without a history, you cannot anticipate recurring problems.
● Using harsh cleaning products: they can degrade the bellows material.
● Ignoring signs of wear: a small crack today could be a complete break tomorrow.
● Not replacing bellows in a timely manner: continuing to use a damaged component can affect other, more expensive systems.
Recommended frequency depending on the type of installation
Although monthly inspections are standard, there are cases where more monitoring is necessary:
● Harsh environments (high temperatures, chemicals): weekly inspection.
● Heavy workloads or intensive cycles: inspection every 15 days.
● Moderate use and stable conditions: monthly inspection is sufficient.
The value of traceability in bellows maintenance
Recording each inspection, detected anomalies, and corrective actions taken allows for:
● Analyzing wear patterns.
● Optimizing maintenance frequencies.
● Improving the selection of materials and manufacturers.
● Making preventive, not reactive, decisions.
A monthly control sheet or a maintenance app can be great allies in this process.
Professional maintenance vs. In-house maintenance
Although basic maintenance can be performed in-house, there are situations where it is preferable to hire experts:
● When there are recurring signs of failure.
● If the bellows are a critical part of a high-security system.
● If a more in-depth technical diagnosis is required.
The support of a specialized manufacturer not only provides expertise but also customized solutions and quality assurance.
A small monthly gesture that makes a difference
Spending a few minutes each month on your bellows maintenance can make the difference between smooth production and a costly downtime. It’s not just about extending the component’s lifespan, but also ensuring the safety, performance, and efficiency of your entire facility.
Operational peace of mind starts with the details, and preventive maintenance is one of them.