In the industrial world, component standardization has long been the norm. However, when the specific needs of a project or application cannot be met with generic solutions, customizing industrial components becomes a key competitive advantage. In this article, we explore how customized components, such as custom bellows, can solve specific problems, improve efficiency, and optimize processes across different sectors.
The challenge of generic components
Generic industrial components are designed to cover a wide range of applications, making them economical and easy to acquire. However, in many cases, standard solutions present limitations such as:
● Limited compatibility: They do not always fit perfectly into existing systems.
● Premature wear: Materials may not be suitable for extreme environments or particular conditions.
● Operational inefficiency: They may not maximize performance in specific applications.
When generic components fail to meet the requirements of an environment or application, businesses face challenges such as increased maintenance costs, unplanned downtime, and reduced equipment lifespan.
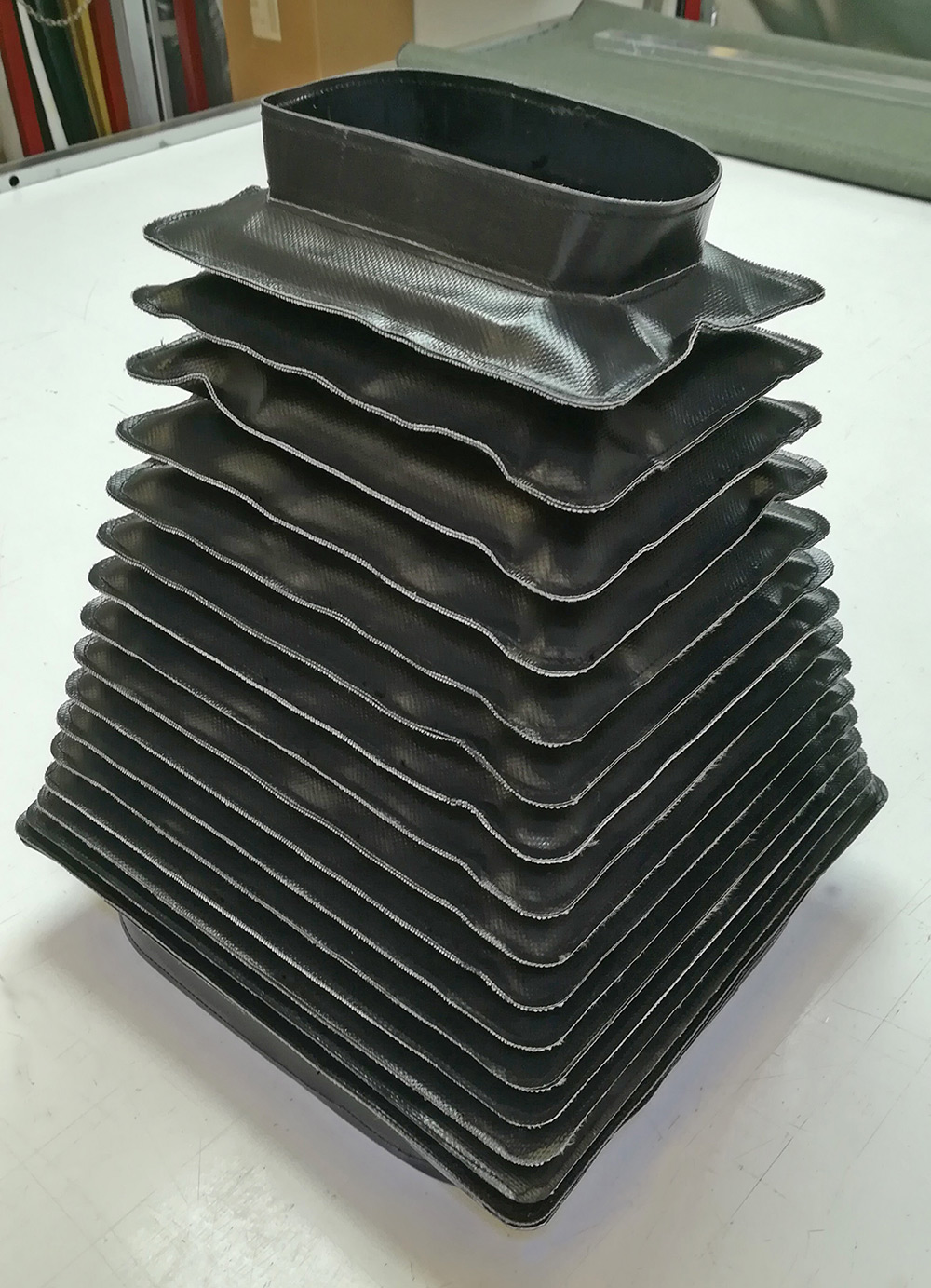
Advantages of customisation in industrial components
1. Perfect adaptation to specific needs
Custom components, such as custom bellows, are designed to perfectly fit the technical characteristics of each equipment or environment. This ensures:
● Full compatibility with specific machinery.
● Optimal performance from day one.
● Elimination of problems arising from improvised adjustments.
2. Improved operational efficiency
Custom components are manufactured to maximise the functionality of the systems in which they are integrated. For example:
● Custom bellows can incorporate specific materials to withstand aggressive chemical environments, extreme temperatures or high humidity, ensuring continuous and efficient operation.
● Optimised design to minimise friction, leaks or interference.
3. Greater durability and lower maintenance cost
Because they are manufactured to withstand the specific conditions of an environment, custom components tend to last longer. This reduces costs associated with:
● Frequent replacements.
● Unforeseen repairs.
● Downtime in production processes.
4. Flexibility in materials and design
Customization allows you to choose from a wide variety of materials, finishes and designs, depending on your needs. For example:
● Specific materials: Silicone, PVC, PU, PTFE, aramid, among others, depending on the application.
● Exact dimensions: To fit into tight spaces or complex systems.
● Specific resistance: Adjusted to factors such as abrasion, pressure or extreme chemical conditions.
5. Regulatory compliance
In highly regulated industries, such as pharmaceutical or food, customized components can be designed to comply with specific regulations (such as FDA, ISO or CE). This guarantees the safety and legality of the final product.
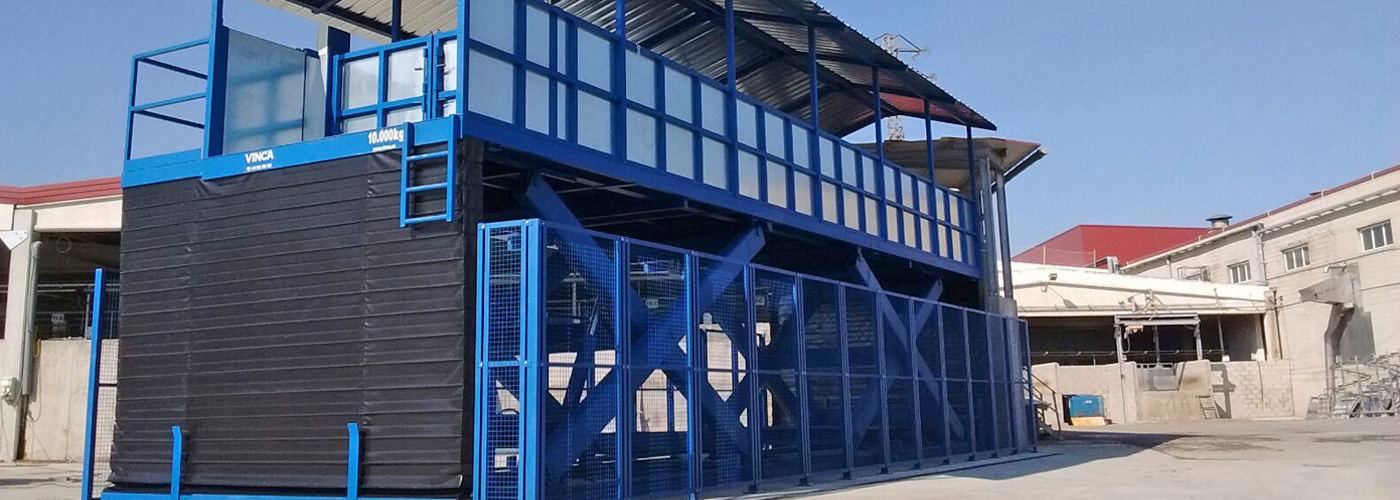
Conclusion
The transition from generic to customized solutions in industrial components, such as custom bellows, offers clear benefits: from improved operational efficiency to greater regulatory compliance and cost reduction. In a competitive environment where precision and reliability are essential, opting for components specifically designed for the needs of each industry is a strategic investment.
Looking for a customized solution for your machinery?
Contact us and discover how our custom-designed components can transform your industrial operation.